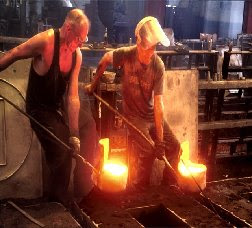
As the customers are looking to buy at ever lower costs, the crucible business is becoming tougher day by day.
Some companies are adopting innovative approaches to tackle this problem. They are working on methods and practices to optimize the life time of their products. Some of the highlights of findings are -
- Long and stable service life of products
- Good conductivity of crucible over the use period
- Protection glaze, which can withstand the longer time in use
- Isostaically pressed to give an even and consistent material structure
Companies, such as Mammut-Wetro have successfully taken up these challenges to reduce their running costs. Mammut-Wetro has a long experience of foundry industry with a technical team that has an extensive knowledge of ceramics and all this is backed by a highly sophisticated laboratory that has facilitated the testing and proving of ideas to attain the desired results.
Mazak Ltd. of Bloxwich, Walsall has been working with the products for many years now, the biggest zinc alloy plant in the UK, using two ton and one ton capacity crucibles. During this period, the company has achieved highly stable operating conditions. The structural unity of the crucibles is maintained even after the complete service life, ensuring the safe and easy removal of a used crucible. According to Keith Sargeant, the Works Director of Striko, Their main advantage has been the consistent quality of products supplied by Striko UK Ltd.
Improving Energy Efficiency
The most energy-intensive process in metal casting is melting. Companies are working on methods and practices to improve melting efficiency as well as to improve yield, thereby reducing the amount of metal that must be melted and hence the production cost.
How to measure success?
- Increased yield and reduced scrap — By improving the yield and reducing scrap, the amount of metal that must be melted decreases and in turn saves energy.
- Melting efficiency - Melting represents 55% of the cost of process energy. Improvement in melting efficiency helps save energy and reduce production costs.