Manufacturing Technology Blog is one of the oldest blogs in its domain focused primarily on metal casting and manufacturing techniques.
Challenges to the US Metal Casting Industry
However, today the US metal casting industry is facing many challenges as never before. The industry is facing the most intense global competition in its history and is severely affected by the increasing costs associated with regulations and other actions by the government, energy prices and health care.
Some of the major challenges to the US metal casting industry are -
Economic Slowdown - Slowdown in economy has resulted in slowest manufacturing recovery in decades. This recession has caused significant job losses and numerous foundry closures.
Foreign Competition - Most of the competitors to the US metal casting industry are free from complex regulations, high labor costs, and enjoy subsidies and government trade protections.
Government Regulations – Several government regulations are badly affecting the US metal casting industry. The most immediate and threatening regulation at this time is EPA's Iron and Steel Foundry MACT. This regulation is expected to be more onerous, expensive and damaging to the future of American metal casting industry.
Energy – The US industry is facing tough challenges with rising energy costs. The industry needs government support for improved efficiency, infrastructure and investments in new technologies.
World Leaders in Casting Production
According to the report, China is way ahead in the race with a reported production of 28.1 million tons in 2006. The country Chinaproduces more castings than the combined production of second through fourtChinah top producing countries. However, China is not the only country that is experiencing growth. 8 out of the top ten couChinantries showed increase in production, of which Japan and India showed a higher growth percentage than China.
According the census, the top ten casting producing nations in 2006 are given below -
China
The gap between China and other countries is increasing. With an increase of 15% over the previous year, the country now accounts for around 1/3rd of the total global production. In 2006, China's total reported production was 28,094,168 tons of metal castings.
United States
In 2006, the metal casting production of United States decreased to 12,454,739 metric tons, showing a decrease of 3.4% over the previous year. It was the first time in last four years that the country's production has not grown.
Japan
Japan showed an increase of 19.1% to stay ahead the fast growing metal casting industry of India. The country's reported production of 7.9 million tons of castings was boosted with an increase of 1.12 million-tons in the production of magnesium and aluminum castings.
India
In 2006, India's production grew by 17.5% to reach 7,179,300 tons of castings. Since 2002, the country's production has more than doubled. During the same year, India surpassed the United States in the production of gray irons.
Germany
ChinaGermany's metal casting production increased by 7.3% in 2006 to reach 5,480,900 tons. The country continues to produce more per plant than other top-10 casting manufacturing nations.
Brazil
After fast growth in 2003 and 2004, Brazil's pace is now steadying in the production of metal castings. In 2006, Brazil's production reached 3,087,045 tons, showing an increase of 4% over the previous year.
Italy
In 2006, Italy's production reached to 2,637,400 tons of castings, showing an increase of 3.8% over the previous year. The country was among one of the top four aluminum casting manufacturing countries in 2006 with a production of 900,000 tons.
France
In 2006, France's production grew by 1.7% to reach 2,381,241 tons. With a slowing automotive market, the nonferrous casting sector suffered a negative growth of 7.5%.
Korea
Metal casting production in Korea grew to almost 2 million tons in 2006, showing an increase of 3.6% over the previous year. It is the eighth consecutive groChinawth year for Korea.
Mexico
Among the top-10 metal casting producing countries, Mexico comes at 10th position with a reported production of 1,675,212 tons. During the year, the country's production decreased by around 6.3% over 2005 and it was the second consecutive year that the country has witnessed a decrease in the number of castings produced.
An Introduction to the Casting Molds
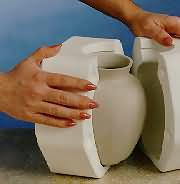
While sand is used as the primary mold material, there is a metal that is used as the mold. Typically, a cast meehanite or iron is used as the mold material and sand is used to make the objects. The cavity surface is usually covered with a thin layer of material (either sodium silicate or clay), which is heat resistant.
Usually the casting molds are pre-heated to a temperature of about 3920 F before the metal is pored into the cavity. The design of cavity for these casting molds does not works on the same principle of shrinkage like in sand casting molds. This is due to the fact that casting molds heat up and enlarge during the pouring process and hence the cavity does not require to be expanded as in the case of sand castings. However, care should be taken so as to ensure a right balance as people may use an external source of water for cooling or they may also opt for appropriate radiation techniques.
Types
Casting molds can be broadly categorized into following four types -
- Permanent Casting Molds
- Slush Casting Molds
- Corthias Casting Molds
- Vacuum Permanent Casting Molds
Permanent Casting Molds
Permanent casting molds offer the benefit of lower cost of production for producing a particular part or component. However these molds are not as flexible as sand castings that can be used in a variety of designs and metal patterns.
In the case, there is a production run of more than 1000 components, a permanent casting mold may produce components at a much lower price in comparison to sand casting. In addition, the break even point also depends on the density of the component. Permanent casting molds are preferred over other types of molds for designing highly complicated parts. Typically the part size would be around 50g to 70 kg and the basic materials used are medium and small parts, which are fabricated from aluminum, magnesium, brass and their alloys.
Slush Casting Molds
These types of molds can be defined as a special kind of permanent casting molds wherein the molten metal is not allowed to harden completely. When the desired wall thickness is attained, the still not hardened molten metal is poured out. Slush casting molds are generally used to design void ornamental objects, such as lamps, candlesticks and statues.
Corthias Casting Molds
This is a kind of permanent casting mold wherein a plunger is used for packing the molted metal through the spure hole. The process permits thinner walls and to produce greater details.
Vacuum Permanent Casting Molds
This is another variant of permanent casting molds that is similar to low pressure permanent casting molds. However, in this case, vacuum is used instead of pressure. As with other low pressure casting molds, this type of mold can be used to produce thin wall castings. In addition, the results are good, as there are no risers used.
Major Cast Metals – Characteristics & Applications
Grey Iron
- Use – 54%
- Characteristics – Heat resistance, damping, economical, low shrinkage and high fluidity.
- Applications - Automobile cylinder block, clutch plate, brake drum, housings and machine tool beds.
Ductile Iron
- Use – 54%
- Characteristics – Strength, wear & shock resistance, machinability and dimensional stability.
- Applications - Crank shafts, cam shafts, valves, brackets, rollers and differential housing.
Aluminum
- Use – 12%
- Characteristics – Strength to weight ration & corrosion resistance.
- Applications – Oil & fuel pumps, automobile pistons, clutch housings and connecting rods.
Steel
- Use – 9%
- Characteristics – Machinability, weldability and strength.
- Applications – Machine parts, valves and gears.
Copper Base
- Use – 2%
- Characteristics – Corrosion resistance and high ductility.
- Applications – Valves, marine impellers and hydraulic pump parts.
Important Rules to Make Good Castings
In the recent few years, we have witnessed a considerable improvement in our knowledge of metal casting methods and techniques. With this enhanced understanding, the list of requirements has been consistently corrected as they have become known. Industry experts have identified several rules and practices, which incorporate the latest technology to manufacture quality castings.
The ten rules that have been identified are proposed as essential, but not, of course, adequate. Manufacturers should follow these rules along with the conventional technical specifications, including type of alloys, strength and traceability via quality standards, and other traditional foundry control measures, such as casting temperature, etc.
Though these rules have not been yet tested on all types of cast materials, there are reasons, which suggest that these rules have general validity and are suitable for all types of metals and alloys. The metals and alloys include those based on zinc, aluminum, cast irons, magnesium, steel, air- and vacuum-cast nickel, titanium and cobalt. In spite of all this, experts believe that these rules will probably benefit all metal casting applications, while some applications will be benefited more, others will be less affected.
Formulated to assist the casting manufacturers and designers, these rules are expected to speed up the process of producing the quality castings right the first time and in the significant reduction of scrap when the casting goes into production. Thus, these rules are expected to help the metal casting industry to raise its quality standards without any considerable increase in costs.
While on the other hand, these rules constitute a draft process, which the metal casting buyers may demand if they wish to make sure that they are buying the best possible casting quality. If the buyers ask their casting sources to follow these casting rules, the reliability and quality of castings would be better than what could be achieved by any quality control casting practice.
Rules -
Provide a Good Quality Melt
Avoid Liquid Front Damage
Avoid Arrest of the Liquid Front
Avoid Bubble Damage
Avoid Core Blows
Avoid Shrinkage Damage
Avoid Convection Damage
Plan Segregation Distribution
Control Residual Stress
Provide Location Points
Learn the Basics of Metal Casting Crucibles

Crucibles Shapes:
Metal casting crucibles come in two shapes – “A” shape and Bilge shape.
Bilge shaped crucibles have the shape of a barrel. The region in the middle part of the crucible is known as bilge, which is the widest part of the crucible and has the maximum diameter. Bilge has greater diameter than the top of the crucible. According to a thumb rule, the # of a bilge crucible reflects the number of pounds of aluminum, which it can hold. In the case of brass and bronze, three times of the # can be held. For example, a # 5 bilge crucible can hold around 5 pounds of aluminum and around 15 pounds of brass. This thumb rule applies only to bilge shaped crucibles.
“A” shaped crucibles have a narrow bottom and a wider top. This types of crucibles have straight sides, which are bent outwards and the diameter increases from the bottom to the top. “A” shaped crucibles are easier to design than bilge ones and hence have lower cost.
Both Bilge as well as “A” shape crucibles can be manufactured in clay graphite and silicon carbide.
Properties of Crucibles:
A crucible should be designed in a way so that it can handle the extremely high temperatures of the molten metal. For this, the crucible should be made of a material, which has a melting point more than that of the material to be melted in the crucible. In addition, the crucible material must have superior strength even in white hot state.
For melting metals, such as aluminum and zinc, a home made steel crucible can be used. However, in this case, the interior surface of the crucible undergoes scaling or flaking, which may pollute the molten metal. It also quickly decreases the thickness of the crucible walls. To solve this problem, a coating of marcote-7 is applied to the inner surface of the steel crucible. The use of steel crucibles is allowed if the contamination due to scales is not serious.
Materials Used:
To design a crucible, the usual refractory materials (such as carbon bonded silicon carbide and clay graphite) can sustain the extremely high temperatures in a foundry. Moreover, silicon carbide is a highly durable material.
Some types of the clay graphite crucibles can be used up to a temperature of 2750 degrees Fahrenheit. Some “A” shape crucibles can be used up to a temperature of 2000 degrees Fahrenheit. These crucibles can be designed to melt silver, gold, bronze, brass, aluminum and zinc alloys.
“A” shaped crucibles have a rough surface finish and have dents along the rims. However, this roughness and dents does not affect the performance of these crucibles.
For proper handling of crucibles, adequately fitted tongs should be used. Poorly designed tongs may result in the damage or the total failure of the crucible. A disk of cardboard or a Plumbago coating should be placed in between the base of the furnace and the crucible.
Recycled Foundry Sand – Uses & Applications
Sand used at foundries is of superior quality, as companies adopt stringent physical and chemical tests to ensure production of defect free castings. Foundries make considerable investments for the quality control of their sand systems with rigorous testing done to ensure consistency.
Though there are several methods of casting, including - die casting, investment casting, and permanent mold casting, sand casting is by far the most preferred casting technique. There are 2 different methods of using sand in metal casting industry -
- As a molding material that forms the external shape of the cast component
- As a core that forms the internal void spaces in products such as engine blocks.
Types of Foundry Sand Suitable for Recycling
Generally two types of binders are used in metal casting industry -
- Clay bonded systems (green sand)
- Chemically bonded systems (resin sands)
Both these types of sand are suitable for recycling and beneficial reuse, however they have different physical and environmental properties.
Uses of Recycled Foundry Sand
Sand from ferrous and aluminum foundries comprise more than 90 % of available sand and is usually best suitable for recycling. Ferrous and aluminum foundries are generally big in size in comparison to other nonferrous foundries and because of the nature of their production, they have more uniform sand streams. This type of sand has a history of uses in different types of construction applications.
Some innovative foundries are finding ways to recycle their used sand. Some other type of non-ferrous sand, or mixed sand streams can be recycled if they fulfill the environmental testing requirements of the regulatory agencies and the required performance standards of the industry.
As with other materials, transportation costs are usually the highest cost factor in the recycling of foundry sand. Considering the cost factor, the best option for the recycling of foundry sand will typically match the volume and characteristics of the foundry sand with businesses and construction projects in nearby areas.
Given below are some of the markets that have the potential to absorb recycled foundry sand from different types of foundries -
- Construction Projects
- Cement Kiln Feedstock
- Flowable Fill
- Manufactured Soils
- Hot Mix Asphalt
- Ready Mix Concrete
- Precast Concrete Products
- Bricks and Pavers
- Grouts and Mortars
- Landill Daily Cover
- Landfill Construction Material
Copper – An Introduction to the Versatile Metal
For around 5 millennia, copper was the only metal known to man, and hence has all the possible metal applications. It was the 1st metal mined and produced by man, and has great significance in older days because of its huge availability. Moreover, copper metal was suitable for crafting weapons, tools, art objects and jewelry.
The wide uses and applications of copper metal over the years of its discovery are well documented. Today, this versatile metal can be seen in objects, as familiar as coins in our pocket, the Statue of Liberty and plumbing products in more than 80 % of all households in the United States.
The metal is invaluable to mankind in a wide array of applications that range from production of alloys to power transmission, to micro-electronics. Each of the thousands of uses of the metal employ a combination of characteristics to help ensure material, which is perfect for the purpose. Good thermal and electrical conductivity combined with strength, ductility and excellent corrosion resistance, are some of properties of this metal that make copper a valuable metal for a range of applications.
The metal is generally found as the multivalent cation, Cu (II), and less frequently as the monovalent ion, Cu (I).
Mining of Copper
About two hundred years ago the UK was an important source of copper for the world and there were mines in Wales and Cornwall. These mines have now closed and today the largest copper mines are located in Chile and North America, which generate several thousands of tonnes of copper every year. The main ores of copper are:
Chalcopyrite
Bornite
Malachite.
These ores are extracted either using traditional mining techniques or through leaching. The pure metal is then retrieved using physical and chemical process.
Recycling
Copper metal is very well suited to recycling and can be remelted again and again with no loss of characteristics. For instance, old copper plumbing taps, pipes, and car radiators are important sources of recycled copper. All these products can be melted down and crafted into new products. In the future, even a tiny amount of copper in the mobile phone will be worth retrieving.
Did you know that copper
Is found everywhere in the Earths' crust.
Is vital to humans. Adults require 2-3 mg in their diet daily.
Is critical to the metabolism of all living organisms.
Provides superior corrosion resistance, excellent electrical and thermal conductivity.
Has good formability.
Is environment friendly and recyclable. More than 80% of copper every mined is still in use.
Has been used extensively in tools and jewelry over 6,000 years ago.
When alloyed with zinc, produces brass.
When alloyed with tin, produces bronze.
Aluminum : Facts Behind the Metal
Bauxite is the main mineral ore of aluminum, which is abundantly available in tropical areas, such as - Africa, the West Indies, South America and Australia. Bauxite contains all types of impurities - mainly metals, such as iron - but comprises of 45 % to 60 % aluminum oxide, or alumina.
In its metallic form, aluminum metal does not occur naturally. It occurs only in combination with other minerals in the form of oxide or silicate compounds that constitute about 8% of earth's crust.
According to estimates, about 29 million tons of aluminum is required to meet the global demand every year. Of this total 29 million tons of total aluminum, around 22 million tons is new aluminum and 7 million tons is obtained by recycling the aluminum scrap. About 25% of the total amount of aluminum used across the world is recycled material.
Fact – 50% of the aluminum cans used today in the US are recycled.
According to estimates since 1972 around 16 million tons of aluminum cans have been recycled. These 785.6 billion aluminum cans if placed end-to-end could stretch to the moon more than 249 times.
Production of Aluminum
Production of aluminum is a two stage process that comprises of various intermediate steps. In the first stage, different mechanical and chemical stages are used to purify the bauxite and recover the alumina with the help of “Bayer Process”.
Once the alumina - aluminum oxide trihydrate - is retrieved, it can be electrolytically reduced (transformed through electrochemical means) into metallic aluminum.
Some Facts -
- Aluminum can be very strong, light (less than 1/3rd of the specific gravity of copper, brass or steel), ductile, and malleable.
- The metal is an excellent conductor of heat and electricity.
- Polished aluminum has the highest reflectivity of any material - even mirror glass.
- The metal can be rolled, cast or extruded into an infinite array of shapes.
- As a packaging material, aluminum as unique barrier characteristics. It resists corrosion and can be recycled again and again, without any loss of quality or properties.
- The metal can be mixed with small, often minute, quantities of other materials, such as - copper, zinc, silicon, iron, magnesium, tin, titanium, lithium, chromium, tungsten, manganese, nickel, and others to create a variety of alloys with very different physical characteristics.
- Aluminum metal is so widely used in todays' modern world that it is very difficult to imaging a world without it. The amazing, unique properties of this fundamental metal give it an extensive array of possible applications, including - transport, packaging, electrical application, medicine, and construction of homes and furniture.
Metal Casting Applications in Japan
As like in Germany, the uses and applications of CAD solid modeling are limited in Japan. Again, as enabling technique for rapid prototyping (RP) machines, a CAD solid model should be designed before a component can be fabricated. The applications of 2-D CAD is very common in Japan.
Mostly a 2D CAD file is transformed to a 3D CAD solid model, then fabricated on an RP machine, however the additional step of designing the solid model increases the cost of the rapid prototyping component. Rapid Prototyping competes with machining for creating prototype components in Japan. In several cases, even complicated geometries can be machined as quickly as parts can be produced using rapid prototyping.
There are a large number of small machine shops in Japan, and the increasing competition in t5he industry makes machining an attractive option in comparison to RP. Low accuracy and surface roughness of components made through rapid prototyping is another drawback of this process. However, with the increasing usage of CAD solid modeling, the applications of rapid prototyping are expected to increase.
The table given below shows some of the Rapid Prototyping systems in use in Japan -

Research & Developments
R&D works for metal casting applications in Japan are mainly focused on the development of materials and software for fabrication of patterns.
Summation
In conclusion, we can say that CAD solid modeling is not used very widely in Japan. In several cases, component designs have to be transformed into solid models before fabrication by a rapid prototyping machine. This results in the increases in the price of RP components. Rapid prototyping can be compared to CNC machining in respect with cost, scheduling, and quality. Inadequate accuracy and surface finishing of parts fabricated using the RP technique are limiting their usage in Japan. Though some of the small companies are are aggressively and successfully using the RP technique for metal casting applications.