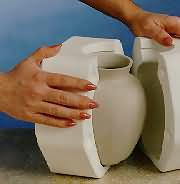
While sand is used as the primary mold material, there is a metal that is used as the mold. Typically, a cast meehanite or iron is used as the mold material and sand is used to make the objects. The cavity surface is usually covered with a thin layer of material (either sodium silicate or clay), which is heat resistant.
Usually the casting molds are pre-heated to a temperature of about 3920 F before the metal is pored into the cavity. The design of cavity for these casting molds does not works on the same principle of shrinkage like in sand casting molds. This is due to the fact that casting molds heat up and enlarge during the pouring process and hence the cavity does not require to be expanded as in the case of sand castings. However, care should be taken so as to ensure a right balance as people may use an external source of water for cooling or they may also opt for appropriate radiation techniques.
Types
Casting molds can be broadly categorized into following four types -
- Permanent Casting Molds
- Slush Casting Molds
- Corthias Casting Molds
- Vacuum Permanent Casting Molds
Permanent Casting Molds
Permanent casting molds offer the benefit of lower cost of production for producing a particular part or component. However these molds are not as flexible as sand castings that can be used in a variety of designs and metal patterns.
In the case, there is a production run of more than 1000 components, a permanent casting mold may produce components at a much lower price in comparison to sand casting. In addition, the break even point also depends on the density of the component. Permanent casting molds are preferred over other types of molds for designing highly complicated parts. Typically the part size would be around 50g to 70 kg and the basic materials used are medium and small parts, which are fabricated from aluminum, magnesium, brass and their alloys.
Slush Casting Molds
These types of molds can be defined as a special kind of permanent casting molds wherein the molten metal is not allowed to harden completely. When the desired wall thickness is attained, the still not hardened molten metal is poured out. Slush casting molds are generally used to design void ornamental objects, such as lamps, candlesticks and statues.
Corthias Casting Molds
This is a kind of permanent casting mold wherein a plunger is used for packing the molted metal through the spure hole. The process permits thinner walls and to produce greater details.
Vacuum Permanent Casting Molds
This is another variant of permanent casting molds that is similar to low pressure permanent casting molds. However, in this case, vacuum is used instead of pressure. As with other low pressure casting molds, this type of mold can be used to produce thin wall castings. In addition, the results are good, as there are no risers used.