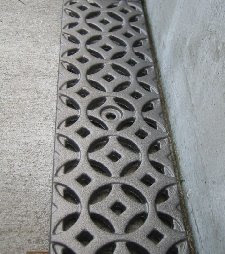
Some general casting design rules are -
- Avoid sharp corners - they may result in hot tearing during cooling.
- Fillets should be used with care – they lead to stresses as they shrink. Radius in the range of 1/8” to 1” is acceptable.
- Use uniform cross sections – they keep the cooling rate relatively uniform and keep off stresses.
- Avoid internal features – they require additional steps in mold making and may cause problems in metal flow.
- Place parting line near corners – they will hide the flash.
- Use straight parting lines wherever possible – It makes the mold making easier.
- Avoid large flats - large flat areas tend to deflection.
- Machining Allowances - allow excess material for later machining of critical dimensions.
- Use a draft angle - A small angle of 0.5-2° on the vertical walls makes it easier to remove the pattern.
- In the designing of cast shapes, an understanding of finished part dimensional prerequisites is essential to attain near net dimensions at most economical cost. The designers should apply as high a tolerance as possible.
- Fix geometric tolerances, like profile of a surface for complex blended surfaces.
And most important of all, consult and work with your casting manufacturer to improve the performance, effectiveness and quality of your casting designs.