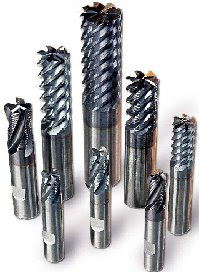
Today, the titanium alloys are used in highly demanding applications, including the static and rotating gas turbine engine parts. Titanium alloys are also used to design some of the most critical and highly stressed civilian and military airframe components. Though highly preferred metal choice for such critical applications titanium alloys tend to be too expensive and this limits their widespread use in industrial applications.
However, improved manufacturing techniques and processes are in development stage that are expected to reduce the prohibitively high cost of titanium alloys. Oak Ridge National Laboratory and industry partners are working progressively to formulate a new and innovative non-melt consolidation process. This new technique is expected to cut down the amount of energy and cost required to produce titanium alloy parts and components by upto 50%. The process will make it viable to use titanium alloys for a multitude of engineering applications, including armor for military vehicles.
Recently, the Oak Ridge National Laboratory used new low cost titanium alloys to design a door for the Joint Light Tactical Vehicle, which is a next-generation combat vehicle. While the main purpose of the use of titanium alloy door was to reduce the weight of the vehicle, it also provided the benefit of decreasing the threat of armor – piercing rounds. Light in weight, the titanium alloy door also enhanced the functioning of door and cut down the overall weight and the fuel efficiency of vehicle, thereby making it even more beneficial for the military and industrial applications.
According to experts, the non-melt approach that comprises roll compaction for directly fabricating sheets from powder, press and sinter techniques to create exact near net shape components and extrusion, provides several benefits over conventional melt processing.
While titanium powder is used to design products in the traditional melt processing method, the powder remains in its solid form during the entire process. This saves a vast amount of energy required for processing, cuts down the amount of scrap by a great amount and allows for new alloys and engineered composites.
Though powder metallurgy has been used to design parts and components for several years, the process is generally not used to fabricate titanium products because of the high cost of traditional titanium powders. New low cost titanium powders are now allowing the researchers to formulate these technologies for titanium.
In coming years, researchers expect the introduction of lightweight corrosion-resistant titanium alloys into several other products, including automobiles that will benefit from the reduced weight and will be able to provide better fuel efficiency.